Types of Plaster Finishes and External Rendering for Buildings
Plastering is a process by which coarse surfaces of wall or ceiling roofs are changed or turned or rendered to provide smoothness. At the beginning, wet materials are spread over the block or brick works and then suitable equipment is used to make the surface smooth level.
The prime purpose of plastering is to obtain hard and smooth surface that could be painted and provide nice aesthetic appearances.

Recently, wall surfaces in modern houses are finished with bricks or blocks or aesthetically pleasing stones to show beautiful appearances.
Wet materials that spread over wall or roof surfaces should not be more than 0.3 cm. However, there are surfaces that irregularities are more than 3cm. In this case under coat which is low cost coarse grain material is used to render the surface followed by finish coat that is thin layer of fine grain materials.
Moreover, walls constructed from irregular and different size stones might require three coating. This is because thick under coat tend to sag due to weight of thick wet plaster.
That is why spreading thin layer and permitting to harden followed by employing second under coat is the best practice as shown in Figure 1. Finally, finish coat is applied for the surface.
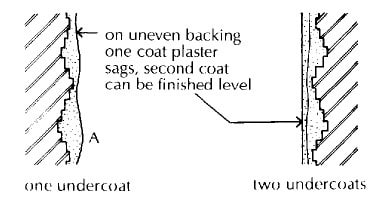
Figure-1: Advantages of Two Under Coat of Plaster
Types of Plaster based on Material Used
Lime Plaster
Lime mixture consists of sand and line that are mixed by 1 sand to 3 of lime by volume. Not only this mixture is used for under coat but also used as finish coat. Lime plaster might be shrink after drying so animal hair of about 5 Kg is used for 1 m2 to avoid lime plaster cracking and shrinking. Lime plaster could be used for ancient structure restoration and rehabilitation.
Cement Plaster
Grey powder Portland cement is mixed with water by the ratio of 1cement to 3 or 4 clean washed sand by volume as an under coat for hard background for example brick block walls and partitions.
Mixture of sand and cement might be plastic and require experienced and skill labor therefore plasticizer or lime is added to the mixture usually by volume ratio of 1cement:0.25 lime: 3 sand or 1 cement to 4 sand with plasticizer.
Plasticizer is a liquid that added to the mixture to ease plaster spreading over the surface.
Gypsum Plaster
Gypsum plaster is widely used plaster materials that could be mined naturally or produced as a by-product. So, important gypsum plaster that is employed as under coat, finish coat, and replaced lime and cement broadly.
Moreover, small expansion of gypsum is considered significant propertied that prevent shrinkages and cracks.
There are various types of gypsum plaster that are produced by heating gypsum to a specific degree for example anhydrous gypsum manufactured by heating gypsum up to 170 Co, hemihydrates gypsum produced by heating gypsum more than 170 Co.
Furthermore, depending on applications for walls or ceilings gypsum plasters can be categorized such as casting, undercoat, finish, one coat and machine applied plaster.
Background Surfaces for Plaster
Type of plaster and its application varies depending on the surface of the wall or ceiling which are set to be plastered. Bricks or blocks with rough and solid surfaces possess means of mechanical adhesion when plaster is applied to the background walls or ceilings.
The mechanical keys which adhere hardened plaster to the surfaces is created after spread wet undercoat plaster is dried. Plaster keys limit or restrain shrinkage of the cement that is principal component of undercoat plaster.
Machine pressed bricks with high density and smooth surfaces absorb suitable amount of water that will help adhering plasters to surfaces. The degree of water absorption by dense smooth surface bricks which assist in plaster adhesion is called suction.
Blocks produced by light weight concrete have large suctions that prevent attaching plasters to surfaces properly. Therefore, it is advised to decrease water absorption degree by either liquid primer or spraying water before plastering.
There are two different solutions for surfaces with low suction include PVA bonding agent and polymer bonding agent. In the former method, polyvinyl acetate is brushed on the surface and plaster is spread over when the PVA is still sticky which creates bond. In the latter, surfaces are treated by combination of silica sand and polymer and the bond is provided by silica sand grain after the polymer is dried.
There are various types of galvanized steel beads and stops which are produced to employ with plaster and plasterboard as angle and stop reinforcement. The beads are used at the junction of wall to ceiling plaster and plaster to other materials.
Galvanized steel utilized as stops to create perfect finishes at junctions of plaster to another material at angles, around windows and doors, and skirting as shown in Figure 2.
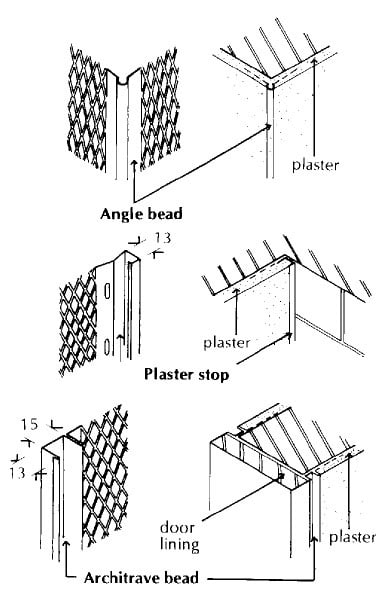
Figure-2: Metallic Beads and Stop for Plasters
Plaster Finishes to Timber Joists and Studs
Plaster spreading on timber lath is an old and traditional technique that used to create level finished surface to the timber floor ceiling and roofs and stud partitions. This method to a large degree replaced by gypsum plasterboard that is why further detailing is not provided.
Gypsum plasterboard is made of hard gypsum plaster that bonded to two heavy papers which prevent damages resulted from handling and installing of the gypsum plaster. It is manufactured with various thicknesses for example 0.95 cm, 1.25 cm, 1.5 cm. and 1.9 cm that applied as dry lining or as plaster background in different size boards.
Gypsum plaster board is widely utilized in ceilings of timber floors and roofs as linings. Plasterboard is considerably cost effective and could be installed and plastered easily.
Another outstanding advantage is resistant to fire because it is incombustible. Nonetheless, poor sound insulation and movement or vibration cracks are drawbacks of plaster boards.
Skirting and Architraves
Skirts are narrow band made around wall base at wall and floor intersection and manufactured strong enough to resist hits. It serves to emphasize wall and floor junction.
There are various types of skirting such as timber, metal, tile, and magnesite. Architraves are mold or forms which are used for decorative purposes installed around doors and windows.
Types of Plaster Finishes used in Building Construction are:
Different types of plaster finishes with different appearances are available as follows.
- Smooth cast finish
- Rough cast finish
- Sand faced finish
- Pebble dash finish
- Scrapped finish
- Depeter finish
- Textured finish
Smooth Cast Plaster Finish
To obtain smooth cast finish, mortar used should be in the ratio 1: 3 [cement: sand]. Fine Sand should be taken to prepare the mortar. For spreading the mortar, skimming float or wood float is best suitable tool. Hence, smooth and levelled surface is obtained finally.
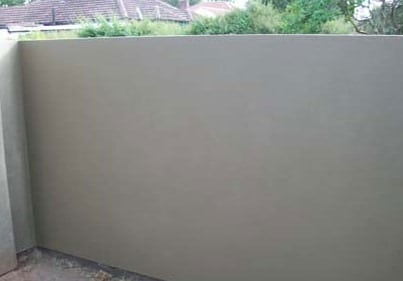
Rough Cast Plaster Finish
Rough cast finish is also called as spatter dash finish. Mortar used to get rough cast finish consist coarse aggregate along with cement and sand. Their ratio is about 1: 1.5: 3. The size of coarse aggregate used is 3mm to 12mm.
Large quantity of mortar is taken by trowel and it is dashed into the surface and levelled using wooden float. Usually this type of plaster finish is preferred for external renderings.

Sand Faced Plaster Finish
To get sand faced finish two coats of plastering is required. For first coat, 12mm thick layer of cement sand mortar in 1: 4 ratio is preferred. The first coat should be provided in zigzag lines. And then it is allowed for curing for 7days.
After that 8mm thick layer of second coat with cement and sand in 1:1 ratio is applied. Level the surface using sponge. Finally take some sand and screened it to obtain uniform grain size. The screened sand is applied on the second coat using skimming float or wooden float. Finally, sand faced finish with uniform grain size of sand is obtained.

Pebble Dash Plaster Finish
Pebble dash finish requires mortar layer of 12mm thickness with cement and sand in the ratio of 1: 3. After plastering pebbles of size 10mm to 20mm are dashed on to the plastered surface. Then press them into the plastered surface using wooden float slowly. After hardening they provide aesthetic appearance to the structure.
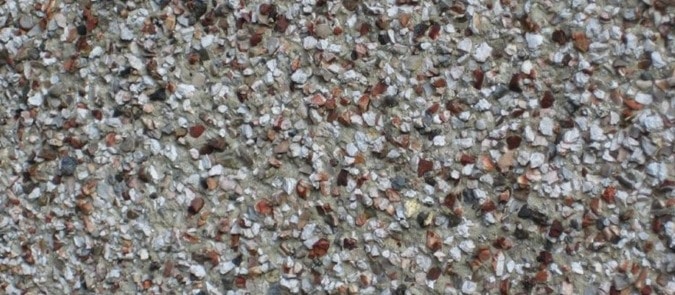
Scrapped Plaster Finish
To obtain scrapped finish, apply final coat of 6 to 12 mm thickness and allowed it to dry. After some time using steel blade or plate scrap the plastered layer up to 3mm depth. Scrapped finish is less liable to cracks.
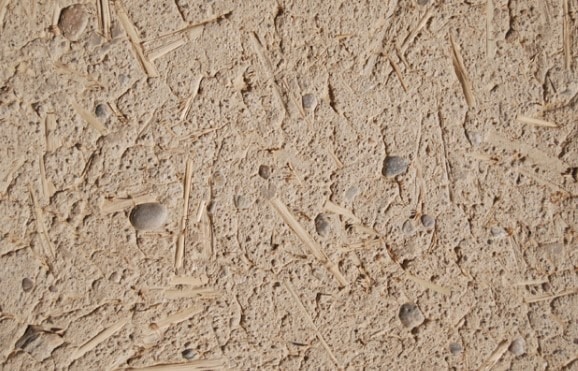
Depeter Plaster Finish
This is also similar to pebble dash finish. But in this case pieces of gravel or flints are used in place of pebbles.
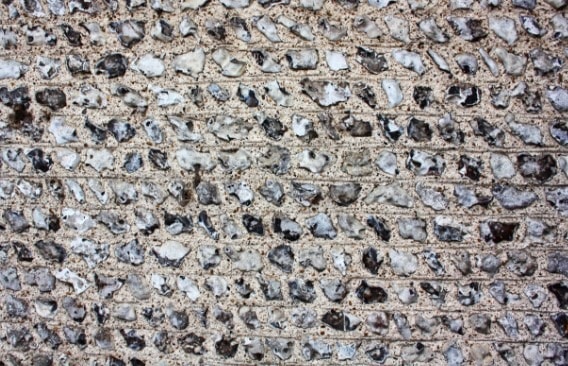
Textured Plaster Finish
Textured finish is obtained from the stucco plastering in which different textures or shapes are made on the final coat using suitable tools.
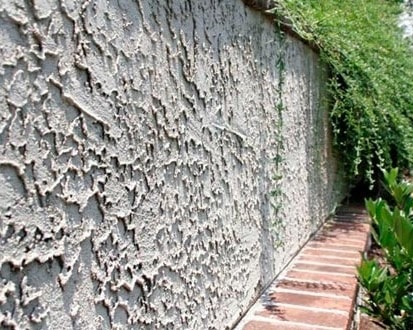
External Rendering of Buildings
Generally, external face of buildings constructed from concrete or clay blocks are not assumed to be pleasing aesthetically and do not provide attractive appearances. That is why the external faces are changed and rendered by two or three coats of lime or cement mixed with natural aggregate and finished textured or smooth.
Moreover, rendering improves and increases wall resistant to penetration of rain fall. Furthermore, external rendering is based on strong bond to the background, utilized mixtures, and surface finish.
No comments:
Post a Comment