Prestressed Concrete Pipes – Types, Uses and Manufacture
Prestressed concrete pipes are widely used around the world and slowly replacing RCC pipes and steel pipes. They have more strength than RCC pipes and economical compared to steel or cast iron pipes. The strength of PSC pipe can be achieved by circumferential prestressing in which a prestressed steel wire is helically wound under tension around the concrete core.
Types of Prestressed Concrete Pipes
Prestressed concrete pipes are classified into two different types as follows:
- Prestressed Concrete Lined Cylinder Pipes
- Prestressed Concrete Non-cylinder Pipes
1. Prestressed Concrete Lined Cylinder Pipes
In this type of Prestressed Concrete Pipes, concrete core pipe is lined by steel cylinder which wrapped with a helix of highly prestressed wire and this wire arrangement is protected by a coat of cement mortar or dense concrete. Steel cylinder contains steel joint rings at its ends which are used to connect two pipes during installation.
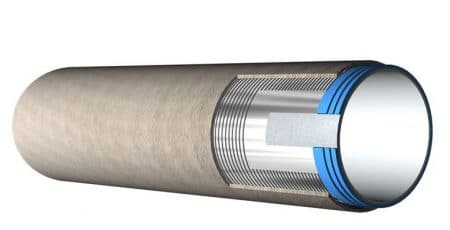
2. Prestressed Concrete Non-cylinder Pipes
Prestressed Concrete Non-cylinder Pipes does not contain steel cylinder between prestressed wiring and the concrete core pipe and this is the only difference between cylinder and non-cylinder type pipes. In this type circular prestressing is directly provided on the concrete core pipe.

Manufacturing Methods of Prestressed Concrete Pipes
Prestressed concrete pipes can manufactured in two different ways which are
- Monolyte Construction
- Two Stage Construction
1. Monolyte Construction
- Monolyte method of prestressed concrete pipes making consists, a vertical steel mold which has an inner shell and outer shell.
- Outer shell of mold consists of longitudinal section which are hold together by spring arrangements. Inner shell of mold consist an expandable rubber membrane.
- In this method, concrete is poured from the top of the mold under high frequency vibration.
- Once the concrete is poured, the longitudinal sections of outer shell are permits the mold to expand and rubber membrane in the inner shell also starts expanding.
- This introduces prestress in concrete and curing is done by steaming in monolyte method.
- In monolyte construction, the whole production process is done in a single stage or cycle.
2. Two Stage Construction
- Two stage construction of prestressed concrete pipes, contains two stages of making and this method can be used to make both cylinder and non-cylinder type pipes.
- To manufacture Non-cylinder type P.S.C pipe, concrete is cast over a tensioned longitudinal reinforcement in the first stage.
- After curing of concrete, in second stage, prestressed wires are wound around the circumference of concrete pipe under tension and cement mortar layer is coated on it.
- Longitudinal stresses induced in first stage are helpful in second stage to resist cracking due to circumferential winding and cracking during installation of pipes.
- In case of cylinder type pipes, steel cylinder is lined with concrete on the inside and this cylinder is wrapped using highly stressed wire.
- After wrapping the wire, a rich cement mortar is coated as a protection layer.
- The wires and the splices are fixed at ends by using tubular fasteners.
- For very high pressures, larger diameter pipes are used which may require double winding of wires and double mortar coating.

Uses of Prestressed Concrete Pipes
Prestressed concrete pipes are used for many purposes as follows:
- To supply water for domestic needs, where water needs high pressure to supply uniformly to distributed mains.
- For Industrial purposes such as re-circulating pipes, cooling water pipe lines etc.
- Used as Pipe lines which carry sewage using gravity.
- Run-off or rainwater collecting pipe lines.
- To construct culverts under roadway, railroad or through any obstruction etc.
- To construct inverted siphons.
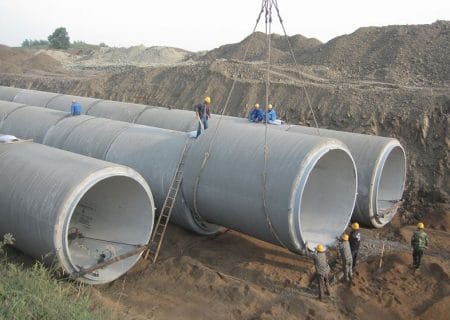
No comments:
Post a Comment