Hybrid Concrete Construction Technique and Structural Actions
Table of Contents
What is Hybrid Concrete Construction?
Hybrid concrete construction is the combination of precast and insitu concrete. Different materials are used according to their strengths and weaknesses to provide simple, buildable and competitive high-quality structures that offer consistent performance.
Hybrid concrete construction can incorporate all the benefits of precasting, (e.g. form, finish, colour, speed, accuracy, prestressing, high-quality, assured covers and dense and properly cured covercrete) with all the benefits of in-situ construction (e.g. economy, flexibility, malleability, continuity and robustness).
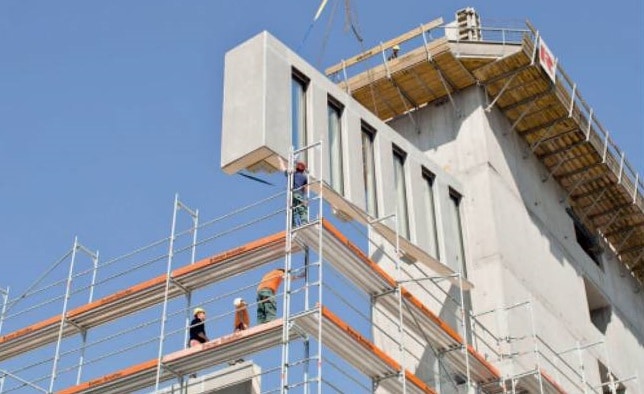
Precast and in-situ concrete can be used together in many different ways to extend the design horizons for architects, engineers and contractors. The precast and in-situ elements can act independently or in combination. In addition a structural element can comprise both precast and in-situ concrete working compositely. Examples are given on the next page.
Numerous hybrid precast and in-situ systems are available and some are used widely.
Structural Action of Hybrid Concrete Construction
1. Independent Action:
Precast cladding adorns mainly in-situ framed buildings. Simple repetitive portions of a structure may naturally lend themselves to precast construction whereas more complicated, less accessible sections may lend themselves to in-situ construction.
2. Combined Action:
Precast units can directly replace in-situ elements, for example stair flights or hollowcore floor units within in-situ frames. Units can be used as permanent formwork, substituting for and largely obviating the need for conventional formwork. This brings the advantages of factory-engineered concrete to site.
3. Composite Action:
In-situ concrete toppings are often added to precast floors for additional strength, stiffness and robustness. In-situ floor slabs can be cast on top of precast downstand beams to give highly efficient composite T beams.
Benefits of using Hybrid Concrete Construction
Time and Cost of Construction
Construction of hybrid concrete structures provides good quality and greater speed during construction making it more economical. Thus, cost of hybrid concrete construction is less compared to normal construction.
Buildability of Hybrid Concrete
Hybrid concrete structural elements are manufactured by skilled workforce. Thus, quality of structural members is good. The use of this concrete also helps to reduce time of construction as design and construction decisions are taken before the start of construction during design stage itself.
Safety during Construction
As most of the hybrid concrete structural members are constructed at factory, it offers more safety to workforce during construction process. The plan for safety procedures for installation of these members can be made based on site conditions and in advance, reducing the chance of accidents at construction site.