Factors Affecting Performance of Concrete During Fire
Inevitably, concrete structures are exposed to fire and high temperature during its life service which creates changes in concrete properties detrimentally and also sometimes causing failure.
Therefore, it is considerably significant to understand factors that control concrete performance during fires.
This article would shed light on the factors that govern the performance of concrete during fire.

Fig.1: Concrete Element Exposed to Fire
Factors that control the performance of concrete during fire include:
- Water to binding material ratio
- Moisture content
- Type of aggregate used to produce concrete
- Supplementary cementitious materials
- Fibers
Water to Binding Material Ratio
One of the factors that influence the performance of concrete during fire is the water to binding material ratio. The smaller the ratio of W/B ration the better the performance of concrete subjected to fire.
It is proven that the decrease of compressive strength and modulus of elasticity of concrete with high w/b ratio (0.6) is greater than that of concrete with low w/b ratio (0.28-0.35). This trend is the same for lightweight concrete and concrete made with cement replacement materials such as fly ash and slag.
It should be noticed that concrete with low w/b ratio would suffer spalling at lower temperature compare with concrete with high w/b ratio.
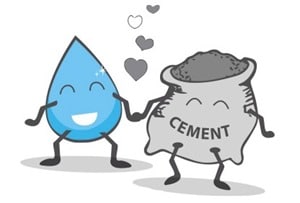
Moisture Content of Concrete
Moisture content directly affects the performance of concrete during fire. It is shown that the increase of moisture content would increase the possibility of concrete spalling due to high pore vapor pressure.
The level of moisture content is based on the relative humidity and nature of coarse aggregate. If the level of relative humidity is greater than eighty percent, then concrete would suffer spalling when exposed to fire.
Type of Aggregate Used to Produce Concrete
Aggregate occupy about 60-70% of volume of concrete, so aggregate properties considerably influence the performance of concrete during fire.
There are three common types of aggregated used to produce concrete namely carbonate like limestone, siliceous such as granite and sandstone and lightweight aggregates such as expanded clay and ceramsite sand.

Fig.2: Carbonate Aggregate for Concrete

Fig.3: Sandstone Aggregate

Fig.4: Lightweight Aggregate
The performance of concrete made from each type of aggregate is different due to properties of these aggregates.
It is demonstrated that, fire and spalling resistance of concrete made from carbonate aggregate is greater than concrete produced using siliceous aggregate. This is because the specific heat of carbonate aggregate is larger than of siliceous aggregate.
The higher the specific aggregate the better the resistance of concrete against spalling due to fire.
Apart from large heat capacity, there are other factors that contribute the enhancement of fire resistance of carbonate aggregate for example durability and ductility.
As far as lightweight aggregate is concern, it is expected to exhibit great performance during fire since thermal conductivity of such aggregate is low and hence its resistance to heat is high.
It is shown based on test that, concrete produced using lightweight or carbonate aggregate exposed to 648.80C would retain compressive strength whereas concrete made from siliceous aggregate would lose half of its compressive strength when exposed to the same degree of temperature.
Supplementary Cementitious Materials
Generally, blending cementitious materials such as blast furnace slag and fly ash improve the performance of concrete subjected to fire. But the influence of cementitious materials is not the same and type of aggregate is also affect concrete performance.
It is demonstrated based on tests that, compressive strength of conventional concrete would be entirely lost at temperature of 1050C whereas concrete produced using cement plus 80% slag replacement would lose around 82% of its compressive strength.
Additionally, supplementary materials would increase the resistance of concrete to spalling during fire. Unlike other supplementary materials, silica fume would outperform by normal concrete when they are exposed to the same degree of fire.

Fig.5: Fly Ash for Fire Resistance of Concrete

Fig.6: Silica Fume for Fire Resistance of Concrete
Fibers in Concrete
By and large, the addition of fiber would improve the performance of concrete exposed to fire. For example, it is shown that the addition of polypropylene increases the resistance of concrete to spalling.
However, it does not enhance mechanical properties of concrete noticeably. It is recommended to mix 0.1 to 0.5 percent of polypropylene to improve spalling resistance. It is advised to use long fibers if it is anticipated that concrete would be subject to high temperature.
Steel fiber is another type of fiber which can be blended with concrete. Spalling resistance of concrete mixed with steel fiber is inferior to that of concrete blended to polypropylene, but mechanical properties of concrete is generally improved.
So, it can be said that the addition of fibers would enhance the performance of concrete subjected to fire.
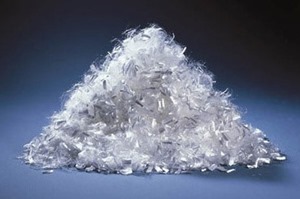
Fig.7: Polypropylene Fiber to Increase Fire Resistance of Concrete
No comments:
Post a Comment