Ventilation in Tunnels -Types of Ventilation Systems in Tunnel Construction
There are various types of ventilation systems in tunnel construction provided to remove dust and poisonous gas during its construction and operation. These ventilation systems in tunnel construction are discussed in this article.
The tunnel construction works are mainly carried out by drill and blast method, which have many safety and health issues due to the emission of dust and many poisonous gasses. Hence it is essential to provide ventilation systems in in tunnel during construction.
The main objectives of providing ventilation systems in tunnel are:
- To provide the working crew an environment of fresh air.
- To exhaust out fumes and gasses, that is injurious to health and explosive in nature.
- To remove the drilling, mucking and blasting gasses emitted.
Ventilation during construction and after completion of tunnel construction is an essential feature that a tunnel should own to facilitate functional, comfortable and a safe tunnel environment for both the road and railway tunnels.

Why Ventilation Systems in Tunnel Construction Required?
When the work is being carried out within the tunnel, each worker has to be supplied with 200 c. ft to 500 c. ft of fresh air constantly. The consideration of compressed air emitted during drilling purpose is contaminated with oil and dust. So this should not be taken as a source of air to play the role of ventilation.
After each explosion, the face is completely covered with air that is full of fumes and dust, which is unfit for breathing. Before he starts to remove the debris of the explosion, the foul air surrounding him must be removed out by any source of exhaustion and get him fresh air.
There exist 30 minutes between the explosion and mucking process, within which the ventilation system installed should clear the tunnel contaminated with poisonous gas and dust and refill with fresh air.
There are mainly three factors, based on which the form and capacity of the ventilation system are dependent:
- The length of the tunnel and its size.
- The amount of explosives used for blasting and their respective frequencies
- The condition and rate of temperature and humidity inside the tunnel
Working Environment inside a Tunnel
The working environment inside a tunnel is contributed by the following factors:
- The dust and the gasses emitted by the tunneling operations
- Exhaust gasses emitted by the diesel operations
- Explosive or organic solvent emitted poisonous gasses. For example Nitrogen oxide, hydrogen sulfide, sulfurous acid gas, carbon monoxide
- Flammable gasses or oxygen shortage gas in the ground. For example, methane, carbon monoxide and hydrogen sulfide
- High temperature and humidity factors
Table-1: Density of Dust Emitted due to Tunneling Works
Tunneling Works | The Density of Dust Formed in mg/m3 |
Excavation | 10 -1000 |
Loading of materials that are excavated | 10 – 1000 |
Mucking | 10 – 100 |
Drilling | 1-50 |
Blasting | 100 – 300 |
Shotcreting | 10 – 200 |
Table-2: Volume of Generated Poisonous Gas in Tunnels

The table below shows the allowable density of dust poisonous gas to control the standard values.
Table.3: Allowable Density Value of Dust inside Tunnel
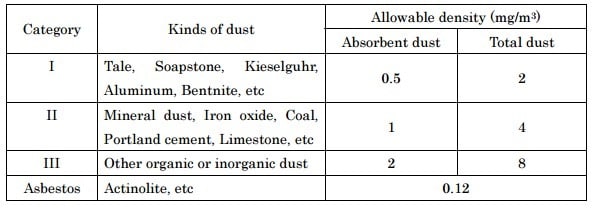
Table.4: Allowable Density of Poisonous Gas in Tunnels

Tunneling Works Safety and Health
To secure safer and healthier environment during the tunneling works, it is necessary to take absolute measures while carrying out the operations of drilling, blasting, excavation, Shotcreting and mucking. Dust, smoke and poisonous gasses inside tunnel can be removed efficiently with the help of a proper ventilation. The government has considered this step to safeguard the health and safety of the labors working in the tunnel.
Types of Ventilation Systems in Tunnel Construction
The methods employed for tunnel ventilation generally depends upon the normal, emergency or congested operation that will be dependent on the actual conditions of the size, cross section, traffic conditions, intermediate ventilation shafts etc.
Types of Ventilation Airflow Systems in Tunnels
Longitudinal Ventilation Airflow Systems in Tunnels
Here the direction of airflow is longitudinal in nature. At the beginning of the tunnel or the tunnel section starting, these moves the pollutant gasses and effluents, that is followed by the fresh air. Then at the end of the tunnel portal or at the tunnel section end, the polluted air is discharged. This is shown in the figure-1.
The configuration of longitudinal ventilation can be either portal to portal, shaft to shaft or from portal to shaft. For transit and railway tunnel, the longitudinal airflow system is used.

Fig.1: Configuration of Longitudinal Ventilation in Tunnels
Transverse Airflow Ventilation Systems in Tunnel
Here uniform distribution of fresh air is created along the length of the tunnel. It is mainly employed in road tunnels. Occasionally it is used for transit tunnels. A consistent level of temperature and the pollutants will be maintained if this system is employed. The system can be either fully or semi-transverse.
Transverse or semi-transverse ventilation tunnel is better than a longitudinal one for the tunnels that are longer than 4 to 5 km.
The ventilation system capability and their choice will depend on the air considerations, the amount of air within the tunnel that too must be calculated based on the traffic conditions, the rate of emission of gases within the tunnel, standards of pollution level, the local standard conditions so that the neighboring environment too is not polluted and harmed.
In the case of railway tunnels, the emergency scenarios of smoke or fire cause is a major concern behind the choice of ventilation. Here mainly longitudinal ventilation is used- that uses ventilation plants at intermediate shafts or at the station adjacent. These may be either combined with exhaust from large caverns.
The ventilation provided can be either Natural or Mechanical ventilation.
Natural Ventilation Systems in Tunnel
When from one portal to next portal of the tunnel, there is a provision of drift, it forms a fair ventilation during the operations involving enlarging. This is when the tunnel length is short. In the case of long tunnels, such natural ventilation will be inadequate and we must design separate mechanical ventilation system.

Fig.2: Natural Ventilation Configuration in Tunnels
The natural ventilation can be configured from portal to portal, shaft to shaft or from portal to shaft. As shown in figure.5. the roadway has an air velocity that is uniform. The temperature and the pollutant level increases at the exit portal or the section end.
If the meteorological conditions of the tunnel go adverse, the velocity, the temperature, and the pollutant level get increased. The pressure differential between the two tunnel portals, that is formed by the differences in the elevation and the ambient temperatures of wind are the chief meteorological conditions.
A sudden change in wind direction or the wind velocity will affect the natural effects along with the vehicle generated piston effect.

Fig.3: Airflow Characteristics in Natural Ventilation System in Tunnels
Mechanical Ventilation System in Tunnels
Mechanical ventilation system employs mechanical devices like electric fans, exhaust, and blowers, which serves the function of removing the exhaust gasses within the tunnel and help in blowing fresh air into the tunnel. Now, whatever be the device employed, there are three main services they can provide:
- Blowing
- Exhausting
- Combination of blowing and exhausting
Blowing Ventilation Systems in Tunnel
As the name tell, fresh clean air is blown to the working face, with the help of pipes. When it flows back to the portal, it takes the dust and gasses with it. This system of ventilation help providing fresh air near the working face with ease. But in long tunnels, these systems have a disadvantage of fogging the atmosphere inside the tunnel when the smoke, dust and foul air move out.
Exhausting Ventilation Systems in Tunnel
The system incorporates an exhausting duct near the working face, into which, the foul air and the dust are let. By this fresh air is maintained within the tunnel, through the entrance. Quick removal of dust and smoke is one advantage of the exhausting system.
The combination of Blowing and Exhausting
The figure below shows a schematic figure of a blowing and exhausting system applied in a combination. This concept is developed, so that the advantage of each system can be combined, bringing a ventilation system of higher performance.

Fig.4: Schematic Representation of Combination of a Blowing and Exhausting Ventilation System in Tunnels
Working: After the explosion or blasting, the exhausting system will operate for a period of 15 to 30 minutes. This will remove harmful air immediately. After this, the blowing system works continuously to supply the fresh air till the next blasting.
From the figure-4, D is the fan and it is supposed to rotate only in one direction. Now the valves A, B, and C are valves that are manipulated either to exhaust from or blow into the tunnel.
Dust Prevention in Tunnel Construction
The dust accumulation within the tunnel is the after effect of conduction the blasting, drilling mucking operations. If the dust accumulated amount is beyond the permissible limit, it creates harmful effects for the people working and to the surrounding environment.
The blasting of rocks as a part of tunneling operation will emit a high amount of silica in the environment. The intake of same will cause a disease called the “silicosis” which is fatal.
Dust Control Methods in Tunnels
The methods used to control dust accumulation are:
- Wet drilling
- Use of vacuum hood
- Use of respirators
Now modern drilling machines are available, that make use of water to drill. Here the area that is to be bored is made wet, resulting in a reduction of dust emission.
The figure below shows a vacuum hood that is used in tunneling work. A hood is fitted to a drill face. This is at the rock face. This is connected to an exhaust pipe. The exhaust pipe takes in the dust formed by the drilling process and that is taken safely out of the tunnel. This reduces no flying of dust to outside.
Another common and efficient method to prevent dust inhalation is using respirators. These are well designed units that are worn by the miners and workers, who are highly exposed to the dusty environment.
No comments:
Post a Comment