Calcium Silicate Bricks or Sand Lime Bricks for Masonry Construction
Calcium silicate bricks are made of sand and lime and popularly known as sand lime bricks. These bricks are used for several purposes in construction industries such as ornamental works in buildings, masonry works etc.
Sand lime bricks are popularly used in European countries, Australia and African countries. In India, these bricks are widely used in Kerala state and its usage is regularly growing.
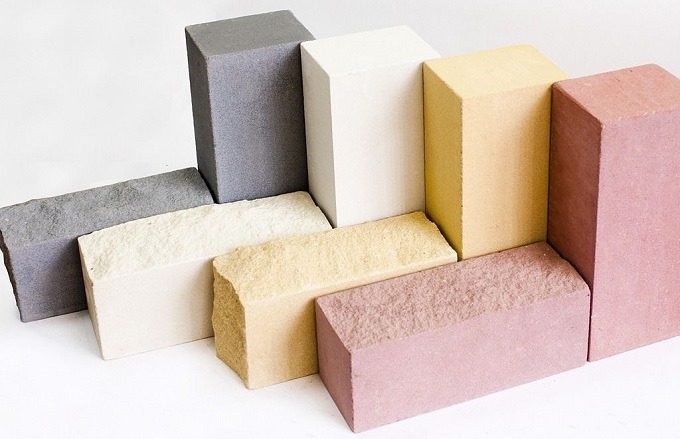
Materials Used for Sand Lime Bricks
The materials listed below are used for the production of calcium silicate bricks.
- Sand
- Lime
- Water
- Pigment
Sand
Calcium silicate bricks contains high amount of sand is about 88 – 92%. It means the properties of these bricks depends upon the characteristics of sand used.
So, the sand used shall be well graded and should not contain any impurities like organic matter, soluble slats etc. the finely divided clay may be present but it is up to 4% only which helps the brick in pressing and provides smoother texture.
Lime
Lime content in calcium silicate bricks varies from 8 to 12%. The lime used shall be of good quality and high calcium lime.
Water
Clean water should be used for preparing calcium silicate bricks. Sea water or water containing soluble salts or organic matter more than 0.25% are not suitable.
Pigment
Pigments are generally used to give color to the bricks. They are added to the sand and lime while mixing.
Total weight of brick contains 0.2 to 3 % of pigment quantity. Different pigments used to get different colors are tabulated below:
Pigment | Color |
Carbon black | Black, grey |
Iron oxide | Red, brown |
Chromium oxide | Green |
Ochre | yellow |
Manufacturing of Calcium Silicate Bricks
In the first step, suitable proportions of sand, lime and pigment are taken and mixed thoroughly with 3 to 5 % of water. Then paste with moldable density obtains.
The mixture is molded into bricks using rotary table press which uses mechanical pressure to press the bricks. The pressure of pressing varies from 31.5 to 63 N/mm2.
In the final stage, bricks are placed in autoclave. Autoclave is nothing but a steel cylinder with tightly sealed ends. The diameter of autoclave is bout 2m and length is about 20m.
After placing bricks in this closed chamber saturated steam pressure is released which is about 0.85 to 1.6 N/mm2. The temperature inside the chamber is raised and the reaction process begins.
Silica content in sand and calcium content in lime reacts and forms crystal like compound called calcium hypo silicate. This process is done for 6 to 12 hours. Finally, the obtained bricks are transported to work place.
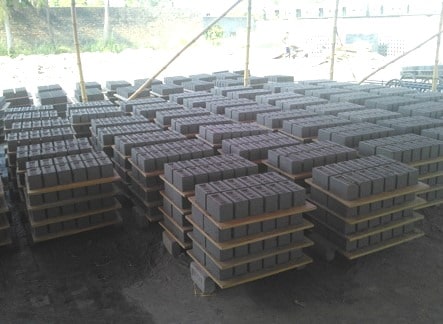

Advantages of Calcium Silicate Bricks
There are many advantages of calcium silicate bricks when used in masonry construction, and they are:
- Mortar required for providing plaster on calcium silicate bricks is very less.
- Color and texture of these bricks is uniform.
- Compressive strength of sand lime bricks is about 10N/mm2. So, they are well suitable for multi storied buildings.
- For constructions in clay soils, these bricks are more preferable.
- Trouble of Efflorescence does not arise in the case of sand lime bricks.
- Not only bricks, blocks and tiles can also be made using calcium silicate.
- Sand lime bricks provides more comfort and accessibility for architects to attain desired shape and designs.
- These bricks have accurate shape and size with straight edges.
- Solar heat effect is reduced on exposed walls made of calcium silicate bricks.
- Colored sand lime bricks do not need any finish to the wall, so, cost reduces.
- These bricks have great fire resistance and water repellant properties.
- Calcium silicate brick walls resists noise from outside.
- Cost of construction gets reduced about 40% of total cost due to following factors.
i. Wastage of calcium silicate products is very less.
ii. Less quantity of mortar is needed.
iii. Thickness of wall can be reduced when constructed using these bricks because of high compressive strength.
Disadvantages of Calcium Silicate Bricks
In some conditions, calcium silicate bricks are not suitable and their disadvantages are:
- If clay is available in plenty, clay bricks are more economical than calcium silicate bricks.
- These are not suitable for laying foundation, because they cannot provide resistance to water for longer period.
- They cannot also resist fire for longer periods so, they are not suitable for building furnaces etc.
- Abrasion resistance of these bricks are very less so, they cannot be used as paving materials.
No comments:
Post a Comment